The field of printing technology has witnessed remarkable advancements and diversification in recent times. In this article, we delve into the intricacies of various printing techniques that play pivotal roles across industries.
From the precision of offset lithography to the versatility of digital printing and the specialized applications of flexography and gravure, each method brings its unique advantages to the table. Furthermore, we explore the interplay between traditional and digital methods, shedding light on their respective strengths and weaknesses.
Additionally, the revolutionary world of 3D printing is examined for its transformative impact on manufacturing and design. This article serves as a comprehensive guide to understanding the multifaceted landscape of printing techniques.
Offset Printing: Precision and Versatility
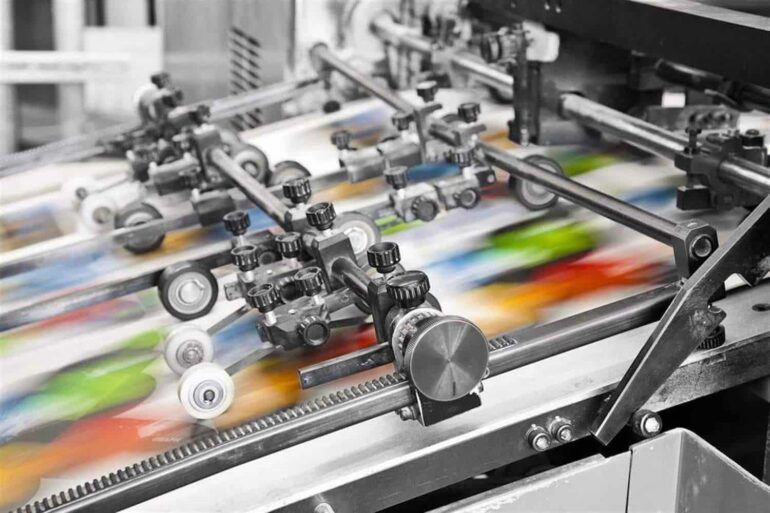
Offset printing, also known as offset lithography, stands as one of the most prevalent and trusted printing techniques in the industry. This method relies on the principle of oil and water repulsion. The image to be printed is transferred from a plate onto a rubber blanket and then onto the printing surface, typically paper. Offset printing is characterized by its exceptional precision, making it the preferred choice for high-quality reproductions, such as books, magazines, and packaging materials.
The offset printing process involves several key components, including a printing press, printing plates, ink, and the substrate. The plates, typically made of aluminum, carry the image to be printed and are treated to attract ink while repelling water. This delicate balance ensures that the ink adheres only to the image areas.
One of the significant advantages of offset printing is its ability to produce consistent, sharp, and vibrant images, making it ideal for tasks that demand the utmost detail and color accuracy. Additionally, offset printing can handle a wide range of paper types and sizes, granting it versatility in applications ranging from business cards to large-format posters.
Furthermore, offset printing can accommodate various ink types, including Pantone and metallic inks, allowing for precise color matching and customization. The method’s efficiency and high-quality output make it a preferred choice for long print runs where cost-effectiveness and image fidelity are paramount.
In conclusion, offset printing is a pillar of the printing industry, known for its precision and versatility. Its ability to deliver consistent, high-quality results across various applications makes it an indispensable tool for professionals in the field. Whether it’s for producing fine art prints or large-scale marketing materials, offset printing continues to play a crucial role in the world of visual communication.
Digital Printing: The Revolution in Reproduction
Digital printing has ushered in a transformative era in the world of printing technology. Unlike traditional methods like offset lithography, which rely on plates and mechanical processes, digital printing involves the direct transfer of digital files onto various substrates. This technology eliminates the need for costly setup processes and allows for on-demand and short-run printing, revolutionizing the industry.
At the heart of digital printing are devices like inkjet and laser printers. These machines utilize advanced technologies to precisely deposit ink or toner onto the substrate, recreating digital images with exceptional clarity and color accuracy. Digital printing offers quick turnaround times, reduced waste, and the ability to personalize each printed piece, making it ideal for applications such as variable data printing, direct mail marketing, and short-run publications.
Moreover, digital printing excels in prototyping and proofing, enabling designers and manufacturers to assess their designs with minimal lead time. This technology’s versatility extends to various substrates, including paper, textiles, plastics, and even ceramics, expanding its potential applications.
One of the remarkable aspects of digital printing is its ability to accommodate variable data, allowing for personalized content tailored to individual recipients. This level of customization is invaluable in marketing campaigns, enhancing engagement and response rates.
In conclusion, digital printing has redefined the printing landscape by offering flexibility, speed, and customization capabilities that were once unimaginable. Its impact extends across industries, from commercial printing to packaging, and continues to evolve with innovations like 3D printing and advancements in ink and toner technologies. As we delve deeper into the digital age, the role of digital printing as a driving force in visual communication remains undeniable.
Flexographic Printing: Precision in Labeling
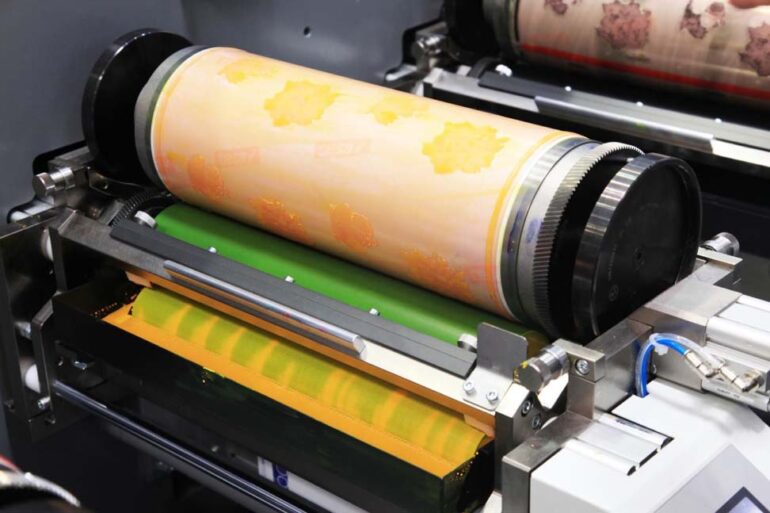
Flexographic printing is a versatile and efficient printing technique primarily used for labeling and packaging applications. This method utilizes flexible relief plates made of rubber or photopolymer to transfer ink onto various substrates. It excels in producing high-quality labels, packaging materials, and more.
The key advantage of flexographic printing lies in its ability to handle a wide range of substrates, including paper, film, and foils. It’s particularly well-suited for digital label printing, allowing for precise and consistent results. The process involves a rotating cylinder that applies ink to the plate and then transfers it to the substrate. This results in sharp, vibrant prints with excellent color saturation.
Flexographic printing is widely used in industries such as food packaging, beverage labeling, and pharmaceuticals due to its speed and cost-effectiveness. Its adaptability to different substrates makes it a preferred choice for custom packaging needs.
In recent years, the integration of digital technologies has further enhanced the precision and efficiency of flexographic printing. This synergy between traditional flexography and digital capabilities has propelled the technique into the modern era, ensuring that it remains a pivotal player in the world of label and packaging printing.
Gravure Printing: Precision in Reproduction
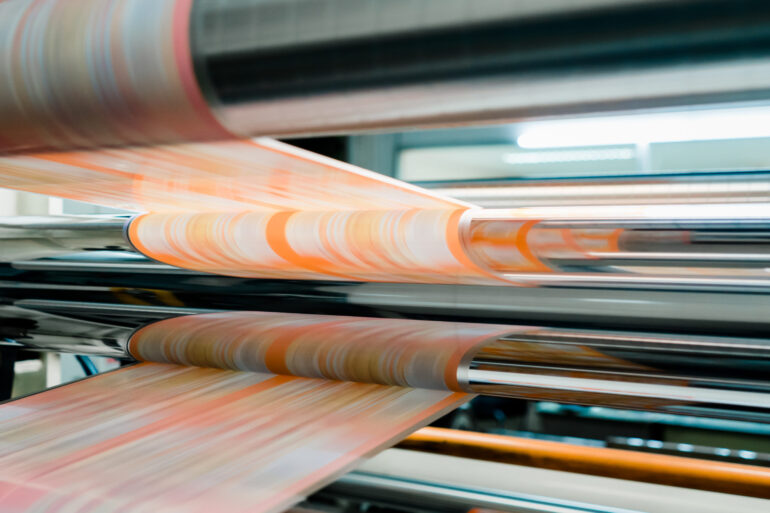
Gravure printing, also known as rotogravure, is a sophisticated and high-quality printing process used primarily in long-run printing applications. It is particularly renowned for its ability to reproduce intricate and detailed images with exceptional clarity and consistency.
In gravure printing, the image to be printed is etched into a cylindrical printing plate, typically made of copper. These cylinders are then submerged in ink, with excess ink wiped off the surface, leaving ink only in the etched recesses. When the cylinder comes into contact with the substrate, the ink is transferred with precision, resulting in sharp and finely detailed prints.
This method is often employed in the production of magazines, catalogs, packaging materials, and decorative printing due to its ability to reproduce images faithfully. Gravure printing’s strength lies in its ability to deliver consistent, high-resolution results over long print runs, making it a preferred choice for applications where image quality is paramount.
Screen Printing: Versatility and Precision
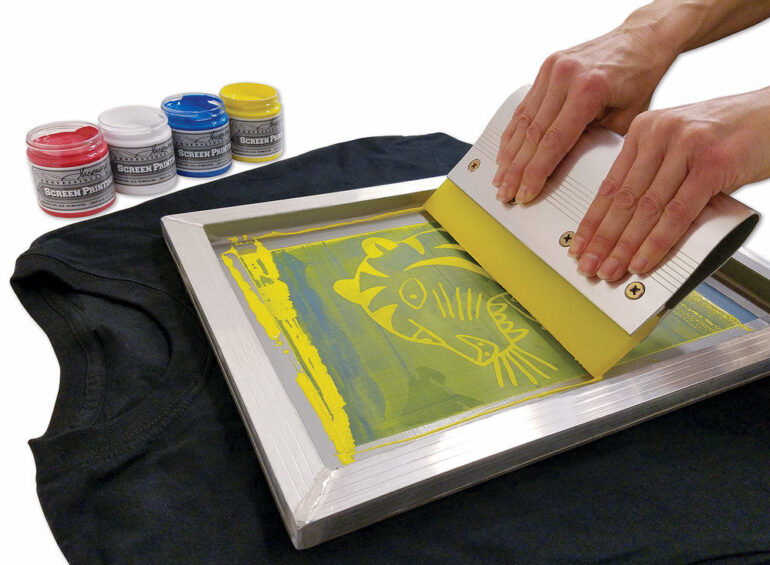
Screen printing, also known as silk screen printing, is a versatile and widely used printing technique characterized by its ability to print on a variety of substrates, including textiles, paper, plastics, and metals. It involves creating a stencil, typically made of mesh stretched over a frame, through which ink is transferred onto the substrate. This method allows for precise and vibrant printing, making it popular for applications like apparel, signage, posters, and promotional products.
Screen printing offers advantages such as durability, color vibrancy, and the ability to print on uneven surfaces. It is an essential process in the world of graphic design and advertising, providing opportunities for unique and eye-catching visuals.
In conclusion, this article has explored different types of printing techniques commonly used in the packaging and printing industry. Each method offers unique advantages and applications, catering to diverse needs in the field of design, branding, and product labeling. From the precision of digital printing to the versatility of screen printing and the high-speed capabilities of flexographic and gravure printing, understanding these techniques is essential for professionals in the industry.
Key Takeaways:
- Digital printing offers precision and customization.
- Screen printing provides versatility for various substrates.
- Flexographic printing is ideal for high-speed production.
- Gravure printing excels in high-quality, long-run jobs.
- Staying updated on industry trends is essential for competitiveness.