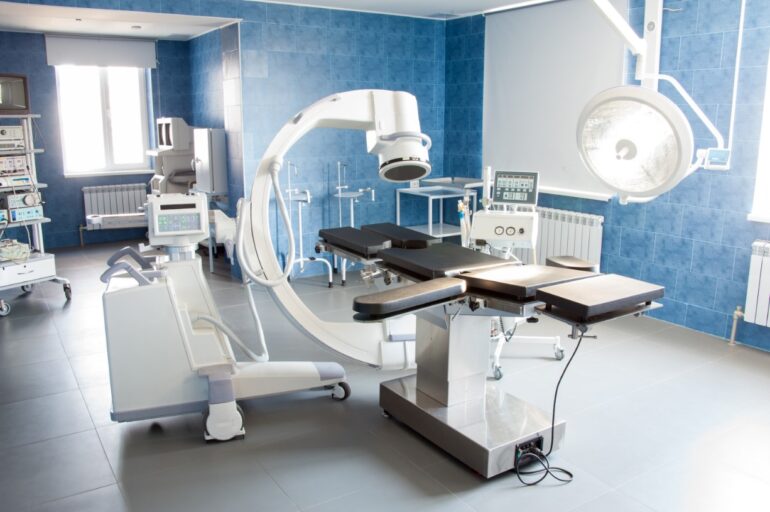
When healthcare institutions consider upgrading or purchasing new medical equipment, the decision-making process must balance cost with quality—a challenge that often entails more than just examining price tags and specifications.
The importance of this balance cannot be overstated as it directly impacts patient care, long-term financial health, and operational efficiency of the organization.
Total Cost of Ownership ─ A Comprehensive Financial Assessment
The first approach in assessing cost versus quality involves a comprehensive analysis of total cost of ownership (TCO). Medera Medical can aid you with just that! TCO goes beyond the initial purchase price to include all costs associated with the lifespan of the equipment, such as installation fees, maintenance, repairs, necessary upgrades, and even training costs for medical staff.
By considering these factors, healthcare managers can gain a clearer understanding of what the equipment will truly cost over its useful life.
For instance, a cheaper model that requires frequent repairs or consumes more consumables can prove more expensive in the long run compared to a pricier, but more reliable, machine. Evaluating TCO allows for a more informed decision, aligning short-term financial constraints with long-term benefits and sustainability.
Looking At Performance Metrics for Optimal Functionality
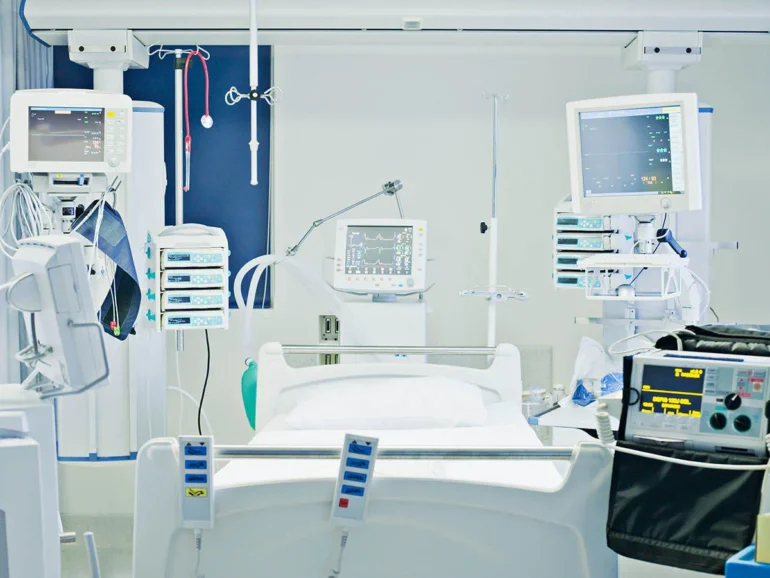
Next, performance metrics serve as another critical dimension in evaluating medical equipment. This involves looking at the equipment’s efficiency, reliability, user-friendliness, and interoperability with existing systems.
A piece of equipment that integrates seamlessly into the hospital’s workflow can significantly enhance productivity and reduce the likelihood of error, which in turn supports better patient outcomes.
Moreover, reliability minimizes downtime due to repairs, ensuring that healthcare services are delivered without unnecessary interruptions. To accurately gauge these performance metrics, decision-makers should solicit feedback from end-users such as doctors, nurses, and technical staff, as well as study comprehensive reviews and case studies from other institutions using the same equipment.
Warranty and Service Agreements ─ Safety Nets in Long-Term Investment
Furthermore, warranty and service agreements are pivotal in assessing the cost-effectiveness of medical equipment. A robust warranty can protect the institution from unforeseen expenses associated with defects or failures.
Service agreements, on the other hand, can vary significantly and need careful evaluation.
They might cover routine maintenance, software updates, and even emergency repairs, which all contribute to the equipment’s longevity and reliability. These agreements often reflect the manufacturer’s confidence in their product and can be indicative of its quality. Negotiating terms that offer favorable coverage can result in substantial savings and peace of mind.
Regulatory Compliance and Future-Proofing Your Equipment
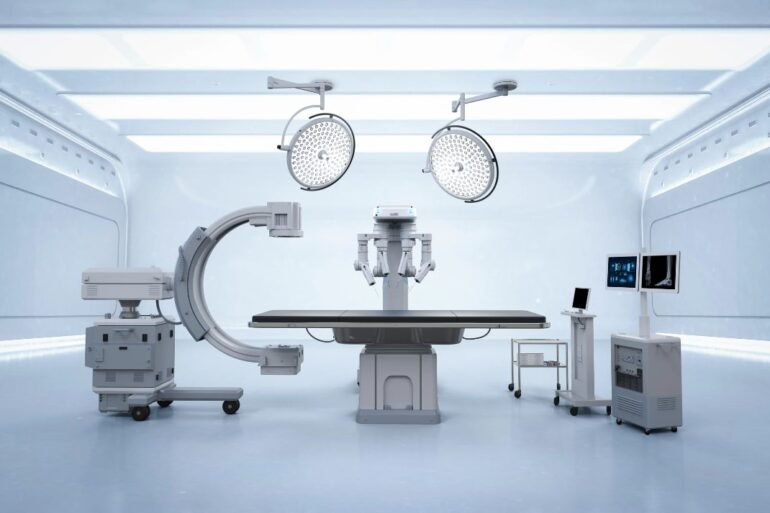
Another often overlooked aspect is the equipment’s compliance with regulatory standards and its potential to adapt to future regulations. Medical technology advances rapidly, and regulatory environments are equally dynamic.
Purchasing equipment that not only meets current standards but is also capable of adapting to new ones can prevent obsolescence.
This forward-looking approach ensures that the equipment will serve the healthcare facility’s needs longer, providing a better return on investment. Regular dialogue with manufacturers about future upgrades and enhancements can provide insights into the potential longevity and relevance of the equipment in a rapidly advancing field.
Assessing the Manufacturer’s Reputation for Quality Assurance
Lastly, the reputation and track record of the manufacturer play a crucial role. Manufacturers with a proven history of quality products and positive post-sale support are more likely to deliver equipment that meets or exceeds expectations.
Investigating the manufacturer’s history, including any past recalls, lawsuits, or frequent complaints, can provide valuable insights into the reliability and quality of their products. Engaging with other healthcare providers for firsthand accounts of their experiences with the manufacturer can also inform the decision-making process.
In conclusion, measuring cost versus quality when purchasing new medical equipment demands a holistic approach. By considering the total cost of ownership, performance metrics, warranty and service agreements, compliance potential, and the manufacturer’s reputation, healthcare institutions can make well-informed decisions.
These decisions not only affect their financial standing but, more importantly, their ability to provide high-quality care. The process requires thoughtful consideration and careful planning but ultimately leads to selections that benefit patients and healthcare providers alike.