Electronic manufacturing companies are under growing pressure to lessen the negative environmental effect of their goods, from waste management to resource sourcing, and to be more “green”.
By optimising performance, efficiency, and longevity, plus incorporating sustainable design, you can reduce any adverse effects on the environment when manufacturing electronics.
The aim of the article is to demonstrate to you how electronic manufacturing companies can adopt several strategies to become more environmentally friendly, and below we have detailed the top five ways that electronic manufacturing companies can be more green…
1. Design for Sustainability
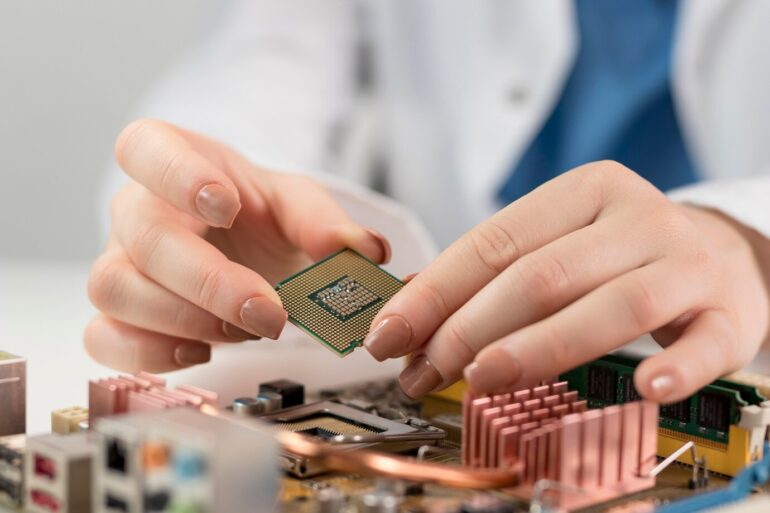
Design for Sustainability (DfS) is an approach that aims to integrate environmental, social, and economic considerations into the product design process. Here’s how electronic manufacturing companies can implement DfS principles:
- Life Cycle Assessment (LCA): Conduct a comprehensive life cycle assessment of the product to identify environmental hotspots and potential areas for improvement. Evaluate the environmental impact of raw material extraction, manufacturing processes, product use, and end-of-life disposal.
- Material Selection: Choose materials that are environmentally friendly, renewable, recyclable, and non-toxic. Prioritise materials with a lower environmental impact throughout the product life cycle. Consider using recycled or biobased materials to reduce reliance on virgin resources.
- Design for Disassembly (DfD): Design products with disassembly and recycling in mind to facilitate end-of-life management. Use modular designs on standardised interfaces to make it easier to disassemble and separate components for recycling. Avoid using adhesives or other fastening methods that make disassembly difficult.
- Durability and Longevity: Design products that are durable, reliable, and built to last. Use high-quality materials and robust construction methods to prolong product lifespans and minimise the need for frequent replacements. Offer repair and maintenance services to extend product usability.
- User Experience: Consider the user experience and usability of the product to promote sustainable behaviours. Design intuitive interfaces, clear instructions, and educational materials to encourage responsible use, maintenance, and disposal of the product.
- Packaging Optimization: Minimise packaging waste by designing packaging that is compact, lightweight, and made from sustainable materials. Use eco-friendly packaging materials such as recycled cardboard, biodegradable plastics, or reusable containers. Avoid excessive packaging and single-use plastics.
2. Energy Efficiency
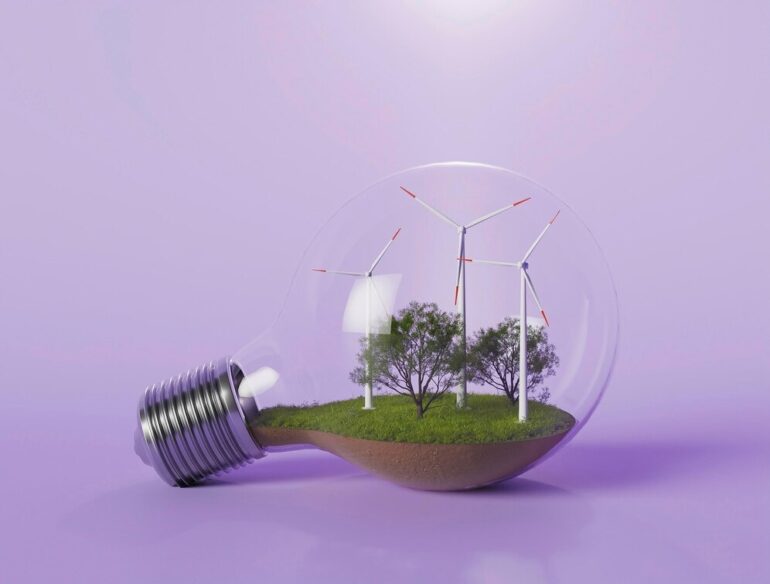
Improving energy efficiency in manufacturing processes can significantly reduce the environmental impact of electronics production, and it’s not just about minimising energy consumption, there is much more that can contribute to a greener operation:
- Energy Audits: Conducting regular energy audits to identify areas of inefficiency and opportunities for improvement is crucial. By analysing energy usage patterns, companies can pinpoint areas where energy is being wasted and develop targeted strategies to reduce consumption.
- Investing in Energy-Efficient Equipment: Upgrading to energy-efficient machinery and equipment can lead to substantial energy savings over time. This includes replacing outdated machinery with newer models that meet higher energy efficiency standards and implementing technologies such as variable speed drives and energy-efficient lighting systems.
- Heat Recovery Systems: Implementing heat recovery systems can capture waste heat generated during manufacturing processes and repurpose it for heating or other energy-intensive operations. By utilising this otherwise wasted energy, companies can reduce their reliance on external energy sources and lower their overall energy costs.
- Renewable Energy Integration: Transitioning to renewable energy sources such as solar, wind, or geothermal power for manufacturing operations can significantly reduce greenhouse gas emissions and reliance on fossil fuels. Companies can install on-site renewable energy generation systems or purchase renewable energy credits to offset their carbon footprint.
3. Recycling Programmes
Establishing comprehensive recycling programmes for electronic waste (e-waste) generated during manufacturing processes and at the end of product life cycles is crucial:
- Internal Recycling Infrastructure: Set up dedicated facilities within manufacturing plants to collect and segregate e-waste generated during production processes. Designate specific areas for storing different types of e-waste, such as electronic components, circuit boards, cables, and plastics, to facilitate efficient recycling.
- Partnerships with Certified Recyclers: Collaborate with certified e-waste recycling companies that adhere to responsible recycling practices and comply with environmental regulations. Establish long-term partnerships to ensure the proper disposal and recycling of e-waste collected from manufacturing facilities.
4. Supply Chain Management
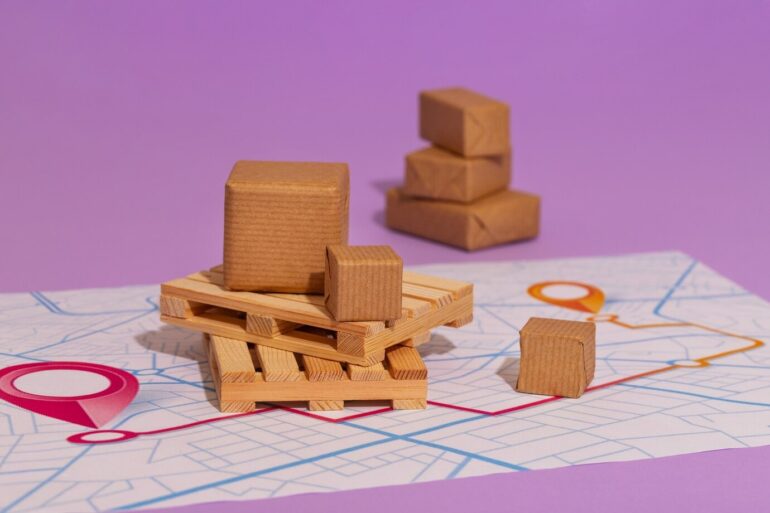
Encouraging suppliers to adhere to sustainable practices can have a ripple effect throughout the supply chain. This includes sourcing materials from environmentally responsible suppliers, reducing packaging waste, and minimising transportation emissions by optimising logistics and transportation routes:
- Supplier Code of Conduct: Develop a supplier code of conduct that outlines expectations for environmental sustainability, labour practices, and ethical standards. Require suppliers to adhere to these guidelines as a condition of doing business with your company.
- Supplier Audits and Assessments: Conduct regular audits and assessments of supplier facilities to evaluate their environmental performance, labour practices, and compliance with sustainability standards. Provide feedback and support to help suppliers improve their sustainability practices.
- Collaborative Partnerships: Foster collaborative partnerships with suppliers to promote knowledge sharing and innovation in sustainability. Work together to identify opportunities for improvement and implement best practices that benefit both parties.
5. Product Life Cycle Management
Implementing strategies to extend product lifespans and promote responsible disposal can reduce environmental impact:
- End-of-Life Management: Design products with end-of-life management in mind to facilitate recycling and proper disposal. Label components with material information to aid in recycling, and provide instructions for safe disposal or recycling at the end of the product’s lifespan.
- Lifecycle Extension: Explore opportunities to extend the lifecycle of products through repair, refurbishment, or remanufacturing. Design products with easily replaceable parts and provide repair manuals and spare parts to support maintenance and prolong product usability.
- Consumer Education and Takeback Programmes: Educate consumers about the importance of recycling e-waste and provide convenient options for returning end-of-life products for recycling. Implement takeback programmes that allow customers to return old electronics to manufacturers for responsible disposal and recycling.
Employee engagement is crucial in any effort to become an environmentally friendly organisation. Educating employees about the importance of energy efficiency and involving them in identifying and implementing new green initiatives can foster a culture of sustainability within the organisation.
Providing training on best practices for energy management and encouraging employees to suggest ideas for improvement can lead to innovative solutions and continuous improvement. By integrating these practices into their operations, electronic manufacturing companies can minimise their environmental footprint and contribute to a more sustainable future.