Choosing the right tool steel for your project can seem daunting. With many options available, making the best choice for your specific needs is crucial. This guide will help you understand the different types of tool steel, their properties, and how to select the right one for your project.
Types of Tool Steel
Understanding the different types of tool steels is crucial for selecting the best material for your project.
- Water-hardening (W-Grades):
- Least expensive
- High carbon content
- Hardened by water quenching
- Best for low-temperature applications
- Air-hardening (A-Grades):
- Medium alloy content
- Hardened by air cooling
- Good balance of toughness and wear resistance
- D-type (High Carbon-Chromium):
- High carbon and chromium content
- Excellent wear resistance
- Suitable for cutting tools and dies
- Oil-hardening (O-Grades):
- Medium carbon and alloy content
- Hardened by oil quenching
- Good wear resistance and toughness
- Shock-resisting (S-Grades):
- Low to medium carbon content
- Designed to withstand high impact and shock loads
- Used in hammers, chisels, and punches
- Mold steels (P-Grades):
- Low carbon content
- Good for plastic mold applications
- Easy to machine and polish
Key Properties to Consider
When selecting tool steel, consider the following properties:
Hardness
Hardness measures a material’s resistance to deformation. Harder tool steels are better for cutting and shaping harder materials. However, increased hardness can lead to brittleness.
Toughness
Toughness is the ability to absorb energy and resist fracture. It’s crucial for tools subjected to shock and impact. Tougher tool steels are less likely to chip or crack under stress.
Wear Resistance
Wear resistance refers to the ability to withstand abrasion and erosion. Tools used for cutting and shaping need high wear resistance to maintain their edge and shape over time.
Machinability
Machinability is how easily a material can be cut, shaped, or finished. Higher machinability means easier and faster production, which is important for efficiency and cost-effectiveness.
Heat Resistance
Heat resistance is the ability to retain properties at high temperatures. For applications involving high heat, like cutting tools, choosing tool steel that can withstand these conditions is vital.
How to Choose the Right Tool Steel
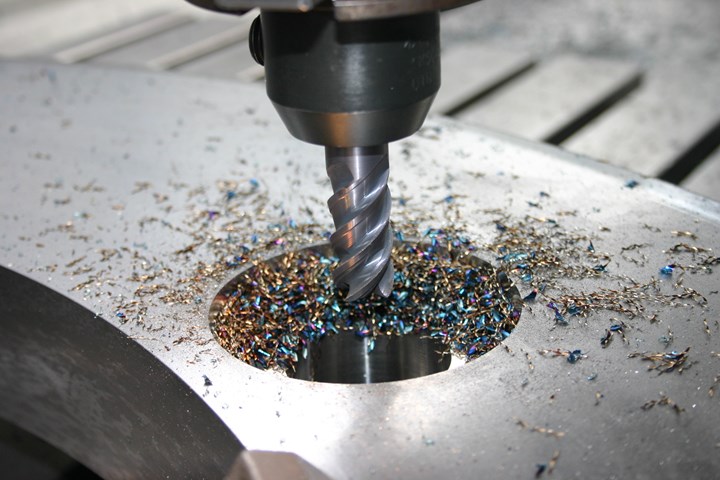
Choosing the right tool steel involves understanding your project requirements and matching them with the properties of different tool steels. Here’s a step-by-step guide:
Step 1: Define Your Project Needs
Identify the specific needs of your project. Consider factors like the type of material you’ll be working with, the required hardness and toughness, and any specific conditions like high temperatures or impacts.
Step 2: Evaluate Tool Steel Properties
Review the properties of different tool steels. Focus on hardness, toughness, wear resistance, machinability, and heat resistance. Compare these properties to your project needs.
Step 3: Consider Cost and Availability
While performance is crucial, cost and availability also matter. Some tool steels are more expensive or harder to source. Balance performance with your budget and timeline.
Step 4: Consult with Experts
Consult with metallurgists or tool steel suppliers. They can provide valuable insights and recommend the best tool steel for your specific application.
Step 5: Test and Validate
Before committing to a large order, test the selected tool steel. Conduct small-scale trials to ensure it meets your expectations and performs well in your application.
Making the Right Choice
Choosing the right tool steel for your project is essential for success. By understanding the properties of different tool steels and matching them to your project needs, you can ensure optimal performance and durability. Always define your needs, evaluate options, consider cost and availability, consult experts, and test before finalizing your decision.