Environmental and Durability Testing helps to easily detect design problems and reduce the risk associated with insurance, warranty, and damage claims. As manufacturers are working hard to increase their goods’ reliability, durability testing is becoming an essential task. When conducted properly, it can help you greatly.
Say, for example, if there is a failure during the transportation of goods, it can lead to big problems. Thus, environmental and durability tests help detect failure during the early stages of manufacturing the product to ensure that it is of great quality. Moreover, identifying any flaws in the product’s design can improve it and help to earn more profits through customer retention and satisfaction.
However, some of the products may turn faulty only under controlled temperature and weather conditions. With this method, you can easily monitor and identify such conditions and go to the root cause. Accordingly, you can address those faults and improve the quality of the products that your customers receive. In this article, we will talk about some things you must know about environmental and durability testing. Check out Custom Microwave to get your products tested.
Standard Of Testing
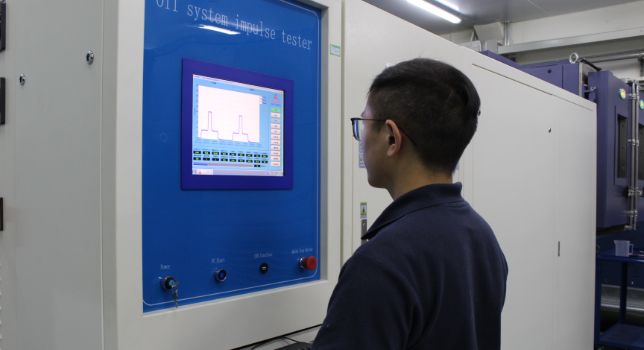
The products’ testing is done as per the standards of UL 50, ASTM, Telcordia, MIL, etc. However, companies can also test as per their norms and conditions. The following tests are performed as a part of the environmental and durability test.
Carbon arc testing:
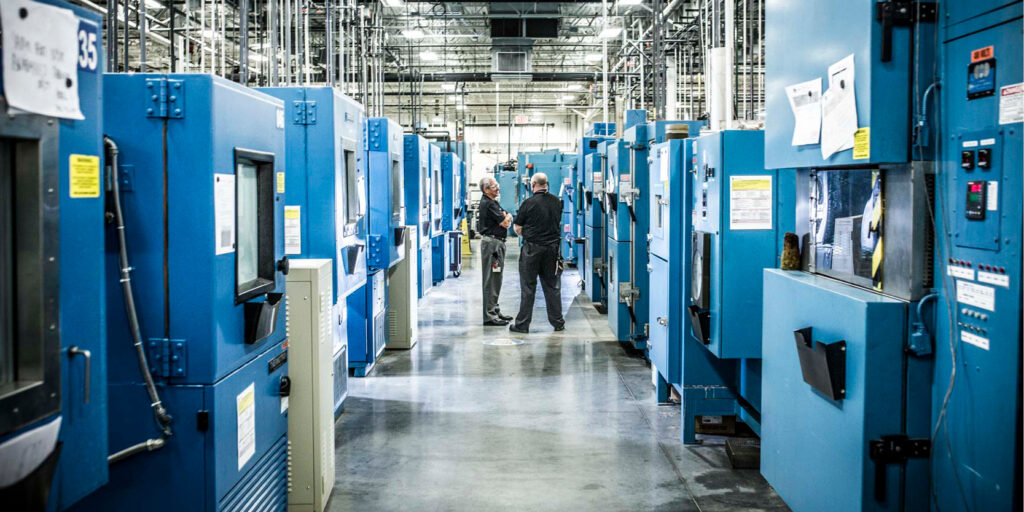
This test is conducted in some of the accelerated weathering chambers designed to check the durability of products and calculate their light-fastness. It is a valuable method of testing that is used to evaluate polymeric materials’ resistance against moisture and sunlight. The devices used in this method use arc light to stimulate the rays from the sun. The heated carbon rods produce UV rays, visible rays, and IR ways when the current forms an arc between them. Renowned labs generally use SWOM that uses an open flame to check your goods’ integrity while complying with the industry’s checking standards.
Cyclic Corrosion Testing:
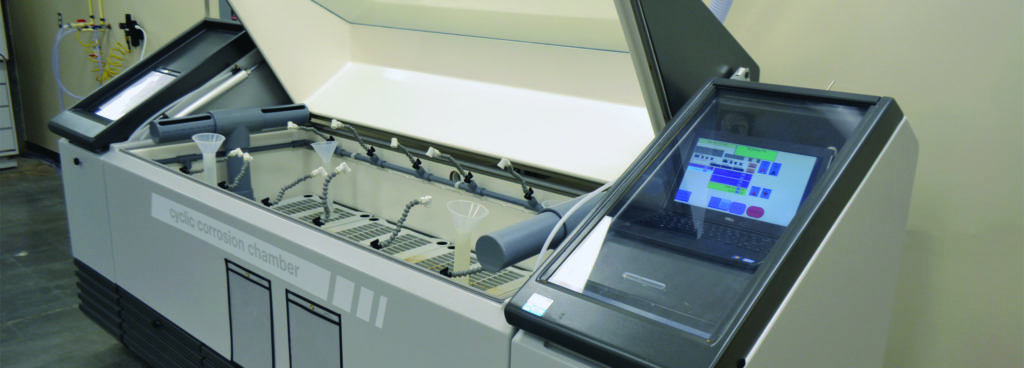
It is a common test that is performed in the automobile industry. This test is performed in a lab and it notes the reaction of various materials used in the auto industry to weather conditions, changes in temperatures, obstacles encountered on the road, etc. These test results help the manufacturers improve their products’ quality accordingly and this produces durable and long-lasting automobiles.
Based on the type of adverse conditions that the manufacturers want to test their products in, CCT is done in several ways. While, in some conditions, the material is soaked in water or other corrosive solutions, in other conditions, the material is made to go through a “dry off” test where it is placed in the external environment and made to go through adverse weather conditions. In some other conditions, solutions are being sprayed on the material to check its integrity. CCT is somewhat complicated and difficult to conduct; however, it is quite an effective test.
Salt Spray Testing
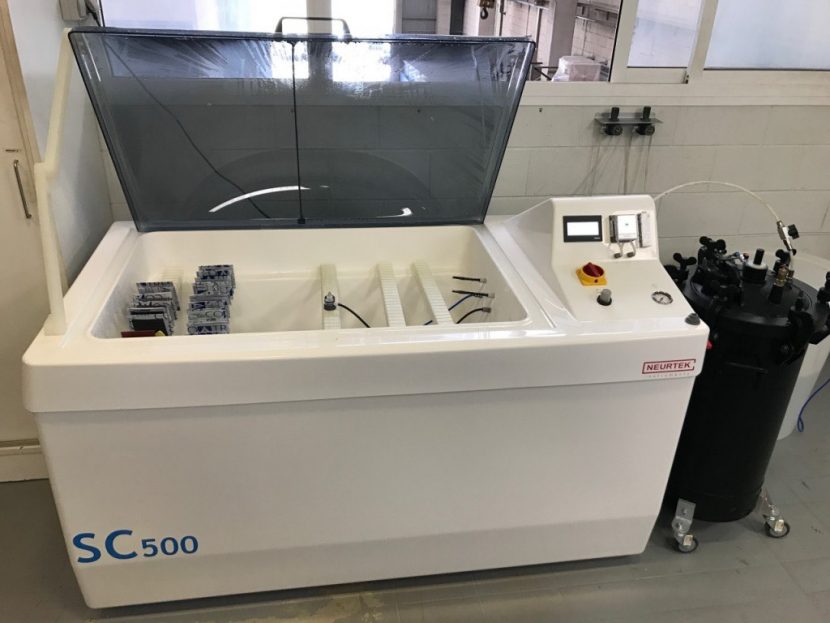
According to leytonfasteners.co.uk, the entire product depends on the fasteners’ durability, no matter the type of weather conditions they are placed in. Thus, it is important to check their durability using this test. The entire product depends on the fasteners’ durability, no matter the type of weather conditions they are placed in. Thus, it is important to check their durability using this test.
In this test, the material is placed in a corrosive saline environment to check whether the surface coatings can endure such harsh environmental conditions. This test is also called salt fog testing, and it dates back to some hundred years. Back in the day, it was used in the HVAC-R coatings industry, and thus it is a must-do test while selecting HVAC-R coatings. This test also approximates the expected resistance and the actual resistance of a material against harsh weather conditions.
This test is generally conducted in closed chambers. In this, a saltwater solution is sprayed over the sample using a nozzle. This solution imitates a corrosive atmosphere. After some time, which depends on the resistance of the material against corrosion, oxides start to appear on the material’s surface. This time period is then noted down and the manufacturers make changes to their products with the help of this data. The more the resistance of a material, the more time it will take for the oxides to form on the surface. The time period can vary in between a day to one thousand hours or sometimes even more.
Temperature/Humidity – Programmable Chamber Exposures
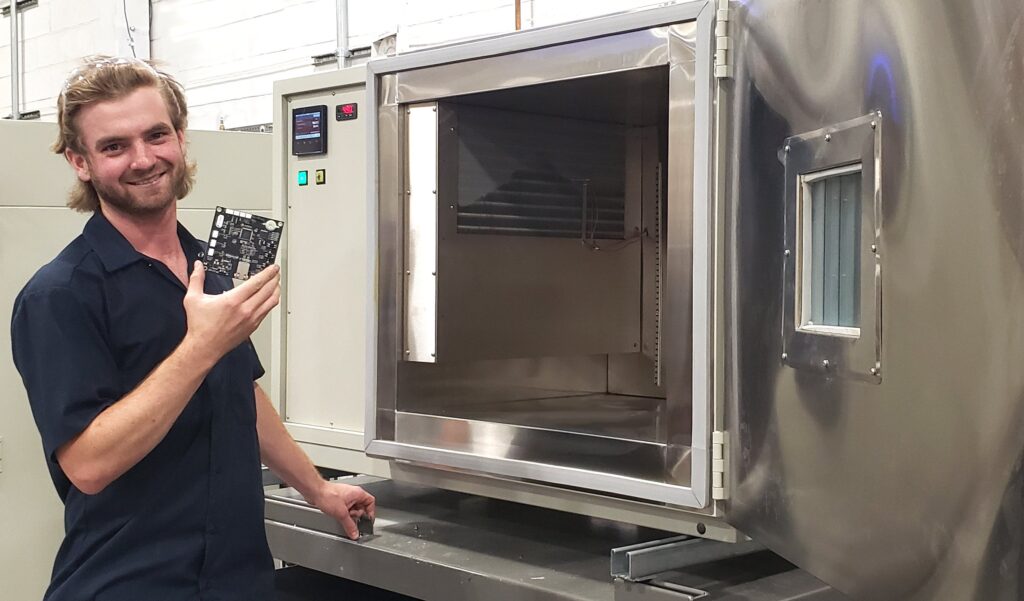
It is the latest technology developed to check the goods’ performance in real-life adverse weather conditions and check their tolerance level to harsh conditions. This test is conducted in chambers that have temperatures between minus forty degrees celsius to one hundred and fifty degrees celsius. They are used to produce atmospheric conditions and test the effect of these conditions on various samples. Industries such as semiconductors, cars, cement, food, etc., use this test to check their samples’ working at adverse weather conditions. It is a must-do test before the companies can launch their final products on the market.
This test delivers a rapid assessment of the product’s performance and helps to improve the quality of the same. It complies with the various norms and regulations to ensure that the test provides accurate results. Products like electronic gadgets, batteries, plastics, etc. are tested using this method
Thermal Aging/Thermal Cycling/Thermal Shock
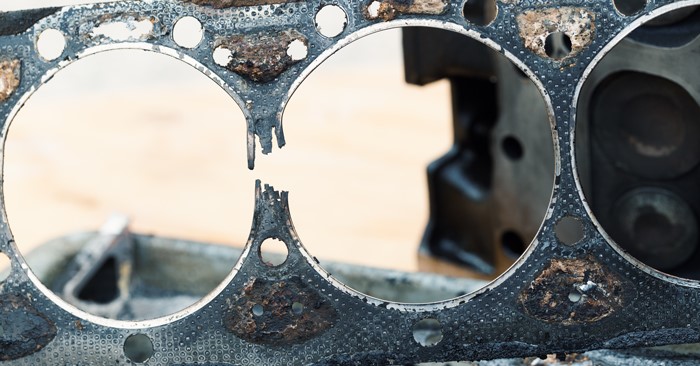
Thermal shock testing is generally used to determine if a specific material can withstand abrupt temperature changes and their reaction to it. The material tested for thermal shock should not experience any physical damage or a decrease in its performance.
Vibration (Single & Multi-axis; Sine, Random, Shock)
Vibration testing is used to determine how a particular product or device responds to vibrations. This testing is carried out to obtain the reliability of products with the help of vibration influences. Durability is the factor that is checked using the method of vibration testing. For instance, all possible environments a car experiences are reproduced during vibration testing.
Final Word
We hope that by now you are aware of the importance of Environmental and Durability Testing and the different types of tests involved in it.